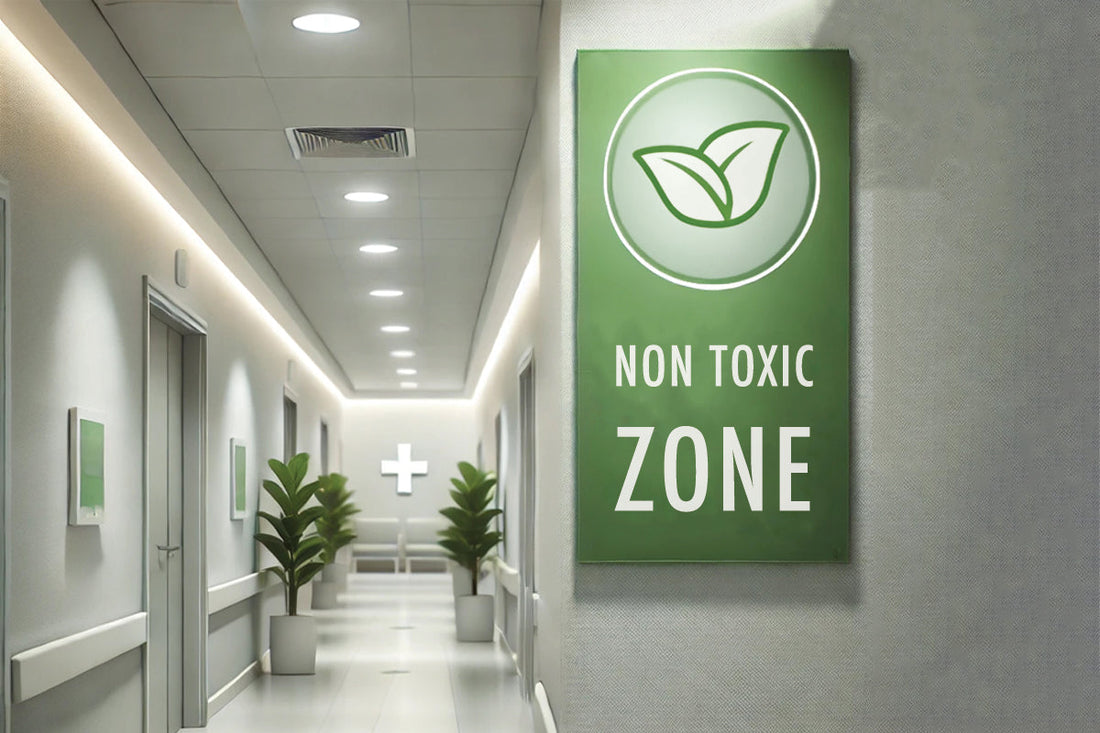
How a Medical Facility Cut Cleaning Costs and Health Complaints in 30 Days
Share
In healthcare environments, cleanliness isn’t optional—it’s critical. But for one regional medical center in the Midwest, their commitment to sanitation was coming at a steep cost. Frequent chemical-related complaints from staff, high product turnover, and rising waste disposal costs were hurting both morale and the bottom line. Looking for a safer and more sustainable approach, the facility partnered with CG Chemicals to pilot a non-toxic, eco-friendly cleaning solution. The results were immediate.
Facility Overview
-
Type: Regional outpatient medical center
-
Size: ~75,000 sq ft
-
Staff: 220 employees
-
Previous method: Traditional chemical cleaning agents including quats, bleach, and ammonia-based sprays
-
Problem areas: Indoor air quality, cleaning supply costs, and staff exposure complaints
The Switch to Non-Toxic Cleaning
The center agreed to a 30-day pilot using CG Chemicals’ non-toxic solution across all departments, including exam rooms, common areas, restrooms, and labs. The implementation involved minimal disruption: cleaning staff received one hour of training, and no additional PPE or ventilation changes were needed.
The product replaced:
-
Ammonia-based window cleaners
-
Bleach disinfectants
-
Multi-purpose sprays with VOCs
-
Harsh floor cleaning concentrates
Results After 30 Days
1. Supply Cost Reduction: -27%
By replacing four separate products with one concentrated multi-use solution, the facility cut monthly cleaning product expenses by over a quarter. Inventory management was simplified, and less space was needed for storage.
2. Elimination of Staff Complaints
Prior to the switch, cleaning-related complaints averaged 6 per week—ranging from eye and skin irritation to allergic reactions. During the pilot, no complaints were filed.
3. Better Indoor Air Quality
Air monitoring before and after implementation showed a 40% reduction in VOCs in high-traffic areas like restrooms and nurse stations. Staff described the air as "noticeably fresher."
4. Shorter Turnover Time
Without the need for extended ventilation or wait times post-cleaning, room turnover between patients was reduced by an average of 3 minutes, allowing for greater scheduling flexibility.
5. Positive Staff Sentiment
A short survey showed that 91% of staff preferred the new cleaning system. Comments cited reduced odor, safer handling, and confidence in sanitation effectiveness.
Conclusion
In just 30 days, this healthcare facility saw measurable gains in efficiency, safety, and staff satisfaction—all from a simple switch to CG Chemicals' eco-friendly cleaning solution. For hospitals and clinics balancing hygiene with health, this case study shows that non-toxic doesn’t mean non-effective.
Shop now or contact us to learn more about our eco-friendly cleaning products!